Spin Weld Joint Design for Spin Welding
CONSIDERATIONS:
1. Parts joint must be on a circular axis. Full rotation of part not required. This frees design typically limited by conventional spin welding.
2. Joint design should allow for sufficient collapse distance, insufficient collapse may cause external welding and possible flash resulting poor weld cosmetic quality when applicable.
3. Determine whether or not final orientation of parts is required.
4. Flash produced during the process should be taken into consideration. However, our process produces a minimal amount inherent to spinning only 1 or 2 revolutions.
5. Parting line must be parallel to the force applied by the driver. Typically, upper part half will be designed for use with drive features (areas for driver to engage part). Optional tooling available that drives part without drive features.
6. Material selection may have an impact on joint design and welder type (orientation or inertial). Part must be designed so that there is no contact (other than the joint area) between the spinning part half and the fixtures part half.
Tongue and Groove Joint Design for Spin Welder
Highly preferred and recommended for part alignment, forging molten plastic, maximum weld strength and “flash” containment.
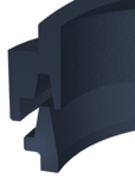
Tongue and Groove
Shear Joint Design for Spin Welder
Useful to maintain part alignment for loading both halves into lower nest and partially contain external flash/particulate
Flanged Shear Joint Design for Spin Welder
Ideal for internal and external flash containment. Good weld strength achieved, but may allow for external flash in the case of multiple revolutions.
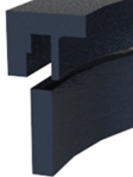
Flanged Shear